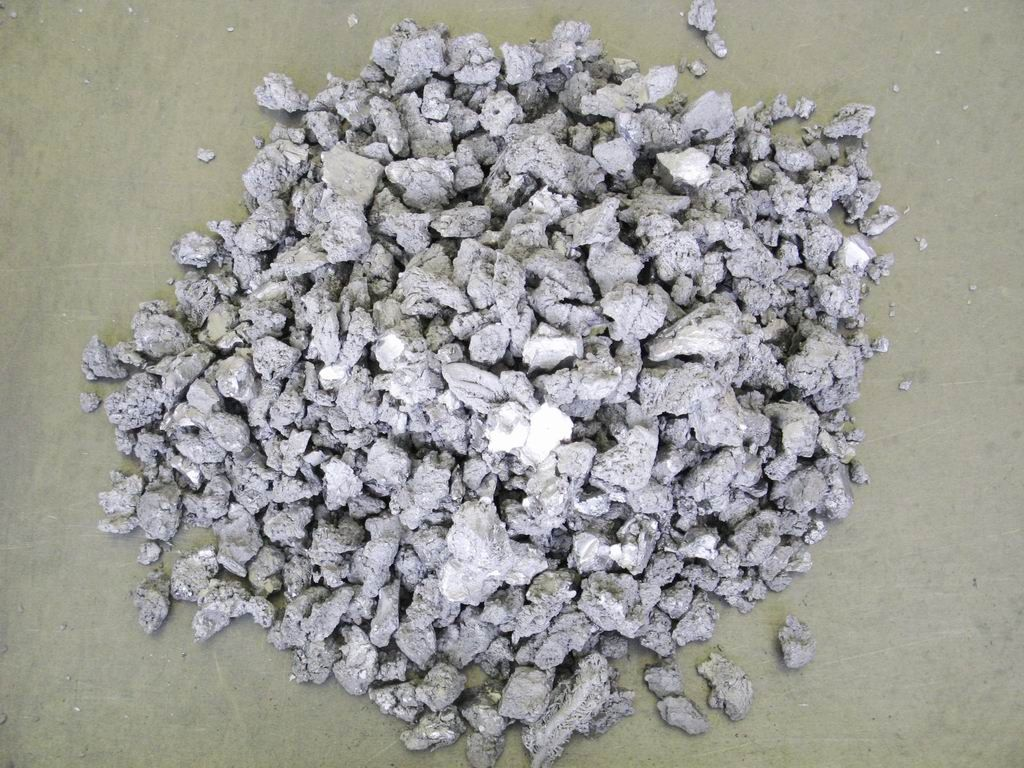
Titanium sponge is a porous form of titanium that is produced during the initial stages of titanium processing. It is a crucial intermediate product in the production of high-purity titanium metal and its alloys. The production process for titanium sponge involves several steps, typically starting from titanium ore, such as rutile or ilmenite. Here’s an overview of the process:
Production Process
- Ore Processing: The titanium ore is first purified to remove impurities. The ore is often converted to titanium dioxide (TiO₂).
- Chlorination: The purified titanium dioxide is then reacted with chlorine gas (Cl₂) at high temperatures to produce titanium tetrachloride (TiCl₄). This reaction also produces various chlorides of impurities, which are removed through distillation.
- Reduction: The purified titanium tetrachloride is reduced using a reducing agent, typically magnesium (the Kroll process) or sodium (the Hunter process). This reduction reaction occurs in a vacuum or inert atmosphere to prevent oxidation and produces titanium sponge along with magnesium chloride or sodium chloride as a byproduct.
- Distillation and Purification: The titanium sponge is then cleaned to remove any residual reducing agent and byproducts. This typically involves washing and leaching the sponge in a series of chemical baths.
- Melting and Alloying: The purified titanium sponge can be melted in a vacuum or inert atmosphere to produce titanium ingots. Additional alloying elements can be added during this stage to produce various titanium alloys with desired properties.
Characteristics and Applications
- Properties: Titanium sponge is highly porous and has a low density. It is highly resistant to corrosion and has a high strength-to-weight ratio.
- Applications: Titanium sponge is used in various industries, including aerospace, medical, chemical processing, and automotive, due to its excellent mechanical properties and corrosion resistance. It is particularly valued in the aerospace industry for manufacturing aircraft components and engines.